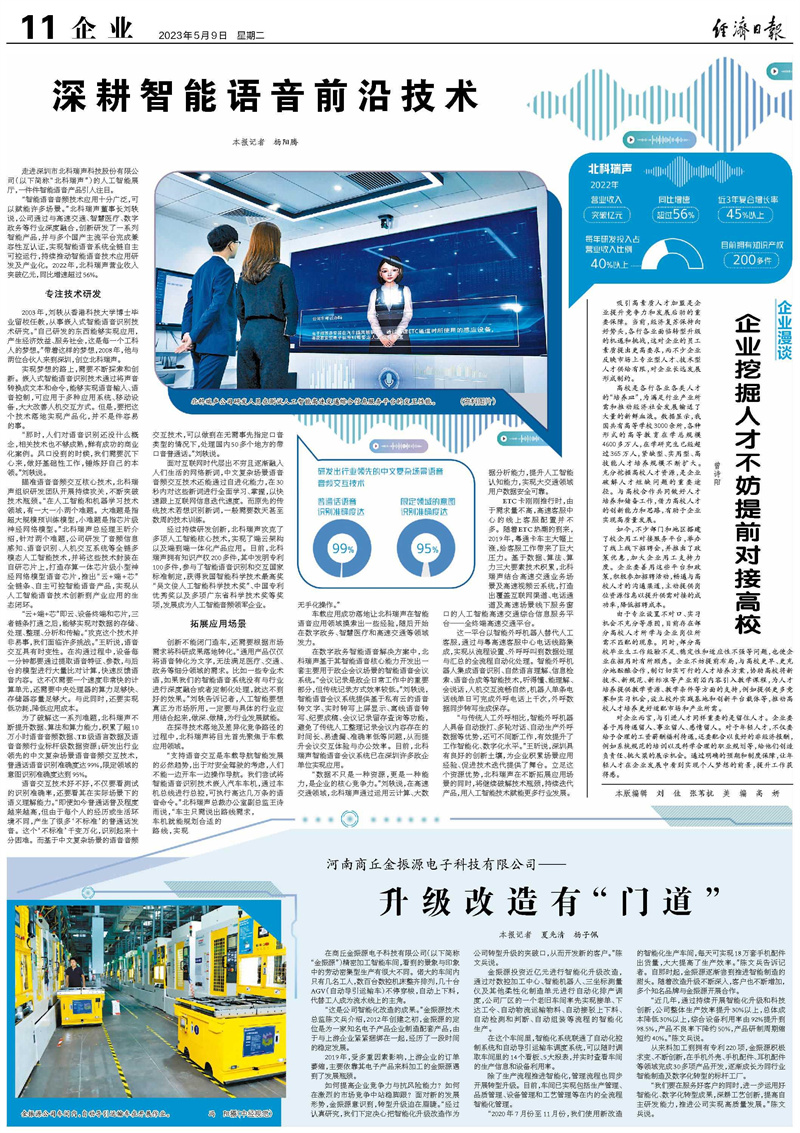
在商丘金振源电子科技有限公司(以下简称“金振源”)精密加工智能车间,看到的景象与印象中的劳动密集型生产有很大不同。偌大的车间内只有几名工人,数百台数控机床整齐排列,几十台AGV(自动导引运输车)不停穿梭,自动上下料,代替工人成为流水线上的主角。
“这是公司智能化改造的成果。”金振源技术总监陈文兵介绍,2012年创建之初,金振源的定位是为一家知名电子产品企业制造配套产品,由于与上游企业紧紧捆绑在一起,经历了一段时间的稳定发展。
2019年,受多重因素影响,上游企业的订单萎缩,主要依靠其电子产品来料加工的金振源遇到了发展瓶颈。
如何提高企业竞争力与抗风险能力?如何在激烈的市场竞争中站稳脚跟?面对新的发展形势,金振源意识到,转型升级迫在眉睫。“经过认真研究,我们下定决心把智能化升级改造作为公司转型升级的突破口,从而开发新的客户。”陈文兵说。
金振源投资近亿元进行智能化升级改造,通过对数控加工中心、智能机器人、三坐标测量仪及其他柔性化制造单元进行自动化排产调度,公司厂区的一个老旧车间率先实现接单、下达工令、自动物流运输物料、自动接驳上下料、自动检测和判断、自动组装等流程的智能化生产。
在这个车间里,智能化系统联通了自动化控制系统和自动导引运输车调度系统,可以随时调取车间里的14个看板、5大报表,并实时查看车间的生产信息和设备利用率。
除了生产流程推进智能化,管理流程也同步开展转型升级。目前,车间已实现包括生产管理、品质管理、设备管理和工艺管理等在内的全流程智能化管理。
“2020年7月份至11月份,我们使用新改造的智能化生产车间,每天可实现18万套手机配件出货量,大大提高了生产效率。”陈文兵告诉记者。自那时起,金振源逐渐尝到推进智能制造的甜头。随着改造升级不断深入,客户也不断增加,多个知名品牌与金振源开展合作。
“近几年,通过持续开展智能化升级和科技创新,公司整体生产效率提升30%以上,总体成本降低30%以上,综合设备利用率由92%提升到98.5%,产品不良率下降约50%,产品研制周期缩短约40%。”陈文兵说。
从来料加工到拥有专利220项,金振源积极求变、不断创新,在手机外壳、手机配件、耳机配件等领域完成30多项产品开发,逐渐成长为同行业智能制造及数字化转型的标杆工厂。
“我们要在服务好客户的同时,进一步运用好智能化、数字化转型成果,深耕工艺创新,提高自主研发能力,推进公司实现高质量发展。”陈文兵说。
|